Industry City Maker Spotlight: Rich Brilliant Willing
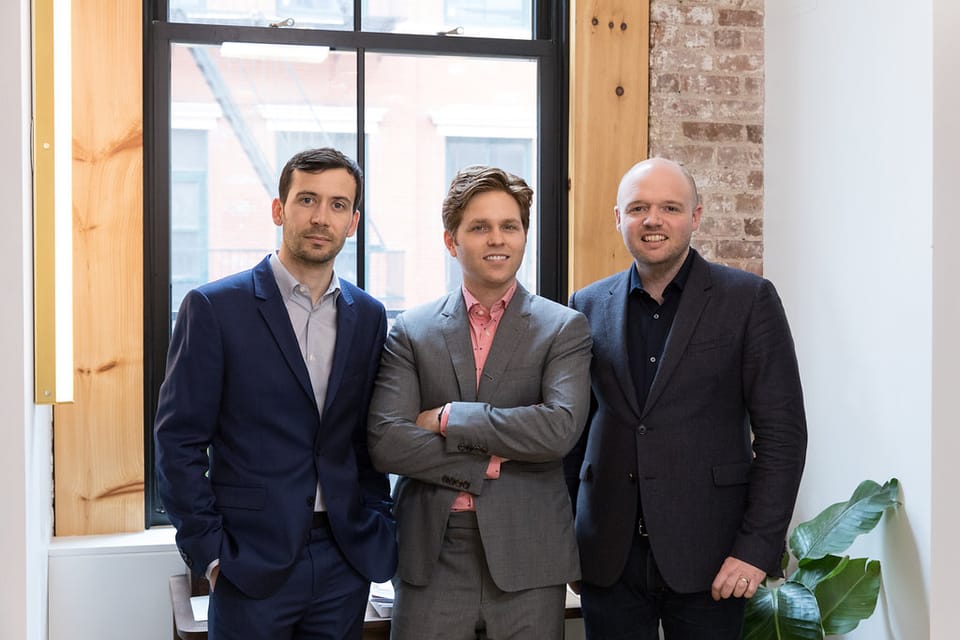
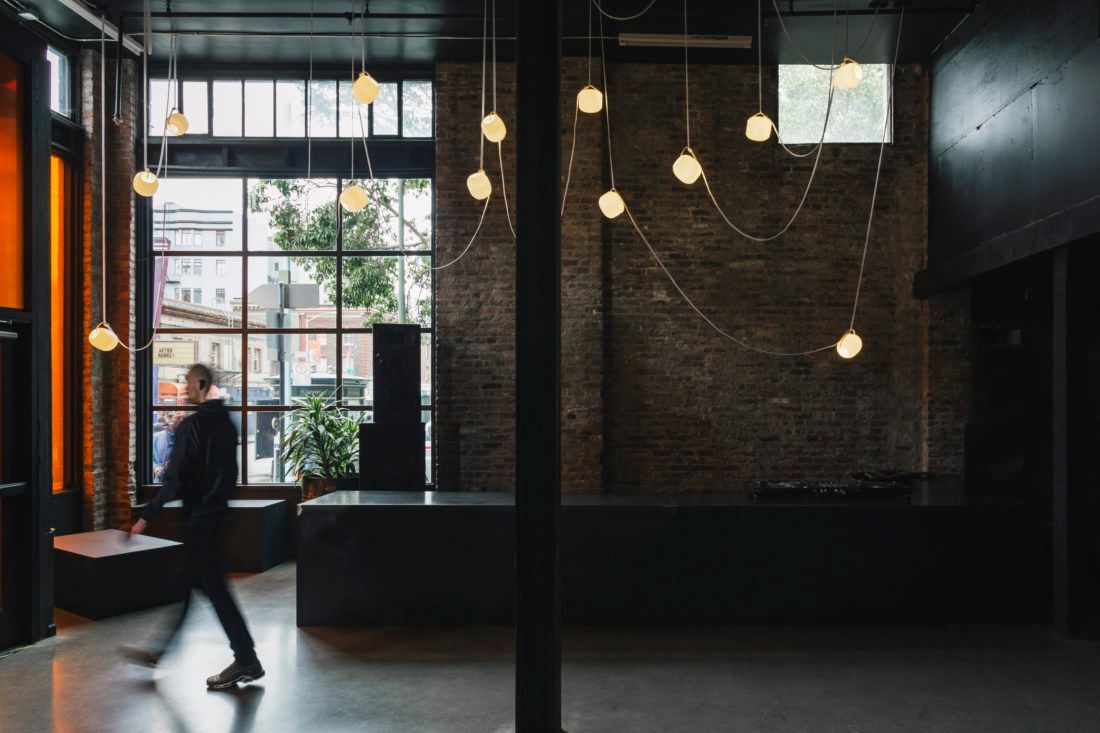
SPONSORED: “We believe in the power of light to create atmosphere, that light has a profound influence on shaping the way we feel.”
That’s how Theo Richardson describes the guiding principle behind the work of Rich Brilliant Willing (RBW), the lighting design firm he founded with partners Charles Brill and Alex Williams (RBW is a play on their last names). All the fixtures they create at their Industry City facility are made with that principle in mind, as tools for architects and interior designers to help them capture the quality of light a specific project demands.
That quality of light is often linked to the shape and function of the fixture itself.
“We create decorative lighting fixtures — sometimes they verge on architectural,” Theo says. By that, he means it’s “a little more minimal in its appearance or even, at times, concealed.” They can even be considered sculptural, as with their Palindrome piece. It has an articulated frame and, at the time of installation, it can be unfolded in a variety of ways. In fact, Theo points out that much of their work is similarly modular.
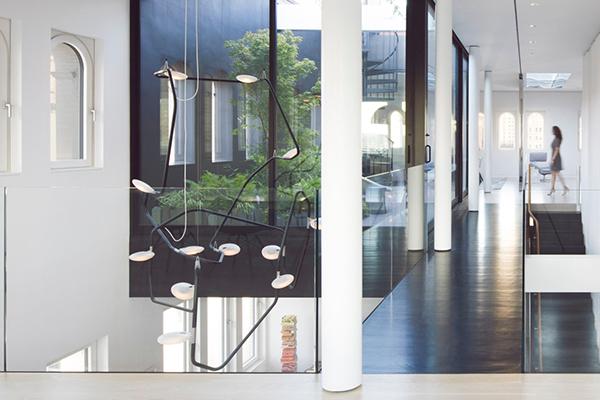
Founded in 2009, the company started in an East Village basement. Theo, Charles, and Alex met while studying together at the Rhode Island School of Design — a fact they affectionately nod to by nicknaming one of their conference rooms Providence. While the three still guide the product-development process, they also each serve a specific function within the company. Theo leads development efforts, Charles serves as Managing Partner, and Alex leads customer relationships.
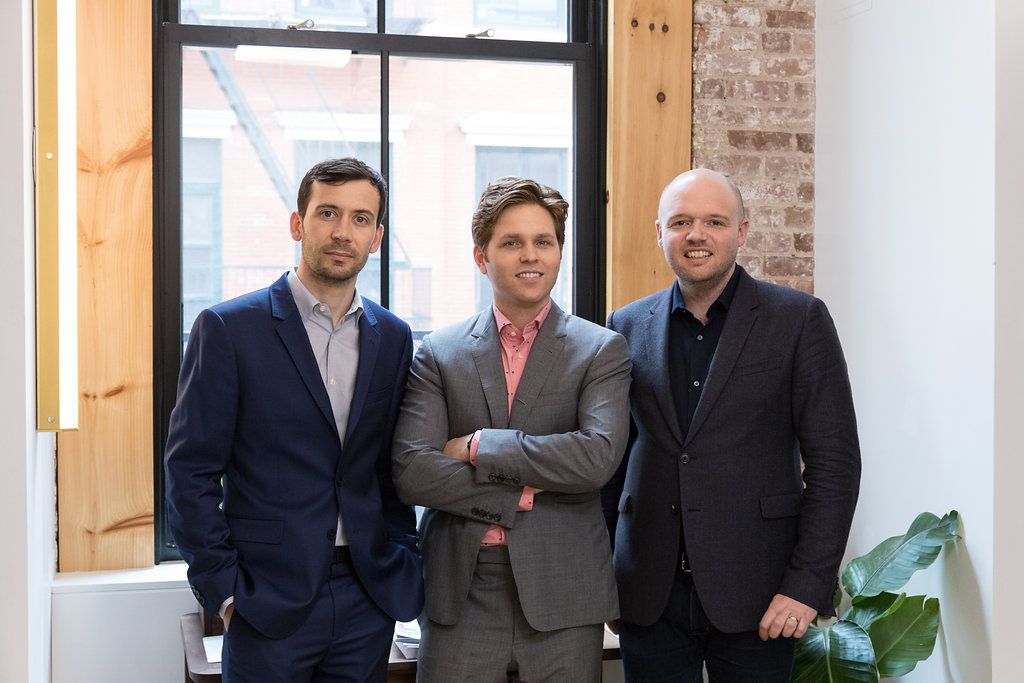
Between 2009 and moving to Industry City in 2016, they had jumped around between various spaces, finally winding up in Gowanus. In listening to them talk about that location, you can hear their affection for it, but they realized it just couldn’t hold them any longer. So, like many other businesses, the search for more room brought them to Industry City.
“There was so much space available that they were able to carve out a floor plan that worked for our needs,” Charles remembers.
Along with the space, they loved the amenities and community Industry City offers, like its incredible food hall and connection with other tenants. They’ve contracted with Keap, another IC tenant, to supply specialty scented candles that they give away as gifts to visitors (including a recent visitor from BKLYNER).
And even the larger amount of space they moved into proved to not be enough. They just completed an expansion and renovation of their offices and production facility, adding another 50% to their square footage — from approximately 8,000 square feet to approximately 12,000 square feet now.
“We used to have two main types of activities — seated desk work and standing assembly,” explains Theo. “We realized we needed a lot more room to be able to accommodate more meeting and community spaces.”
That’s understandable considering that when they came to Industry City, they had eight employees, compared to around 33 now. Many of those additional hires came from recruiting efforts they did through the Brooklyn Chamber of Commerce — which Charles is a member of — and a job placement initiative that Industry City runs with the Southwest Brooklyn Industrial Development Corp. (SBIDC) through the property’s onsite job placement and entrepreneur development center Innovation Lab.
One of those new hires is Ruben Castillo, a native of the surrounding Sunset Park neighborhood. He was brought on in February as a Customer Success Representative and couldn’t be more excited about being a part of Industry City.
“Growing up in Brooklyn,” he says, “I have witnessed this place go through so many phases. The platform Industry City has for small businesses to thrive is amazing. It is filled with diversity and people from all backgrounds. What was once underutilized, worn-down factory buildings several years ago is now the key location to entrepreneurs. The success Industry City has shown Sunset Park only excites me more to see what this place attracts into the coming years.”
The founding trio’s main goal, both in moving to Industry City and in investing in the space, was to bring their customers into their process. They wanted the physical space of their manufacturing facility to more closely mirror the level of the products themselves. As Charles puts it, “the experience is supporting the product.”
In addition, they were thinking a lot about their internal culture and creating a really special space for their people to work in.
To that end, they opened up a bunch of walls and created three large skylights.
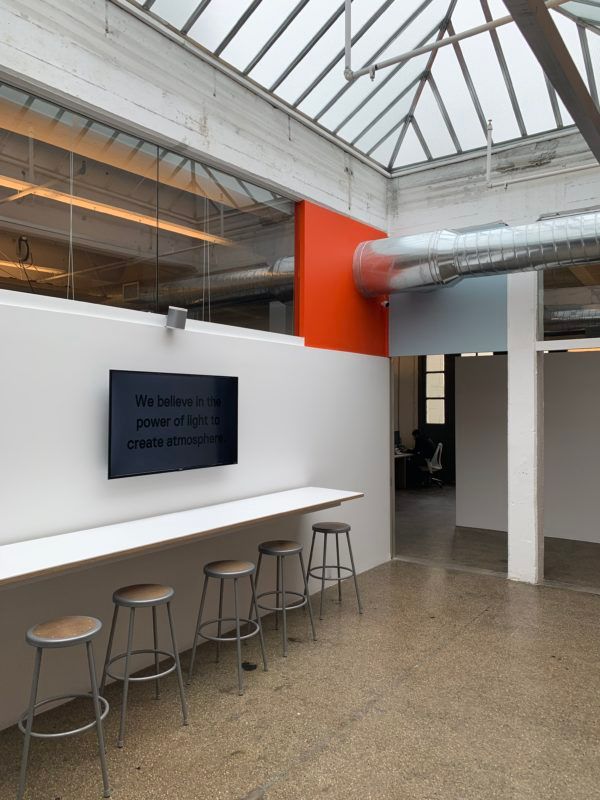
Also, they now have one side of their facility fully devoted to their assembly operation and the other devoted to design and customer service. “If there’s an opportunity we see on one side of the space,” says Theo, “you just walk 20 yards over and talk to your colleague to find ways to refine it.” The public meeting spaces are located between the two halves.
The parts for their products are fabricated through outside partners elsewhere, but final assembly takes place entirely at their Industry City facility. And assembly is anything but simple. “We want to have the most diverse offerings while maintaining the smallest inventory possible,” says Charles. Those offerings — things like options in size, color, input voltage, and dimmer controls — amount to around 15,000 product SKUs all housed on the assembly side of their facility.
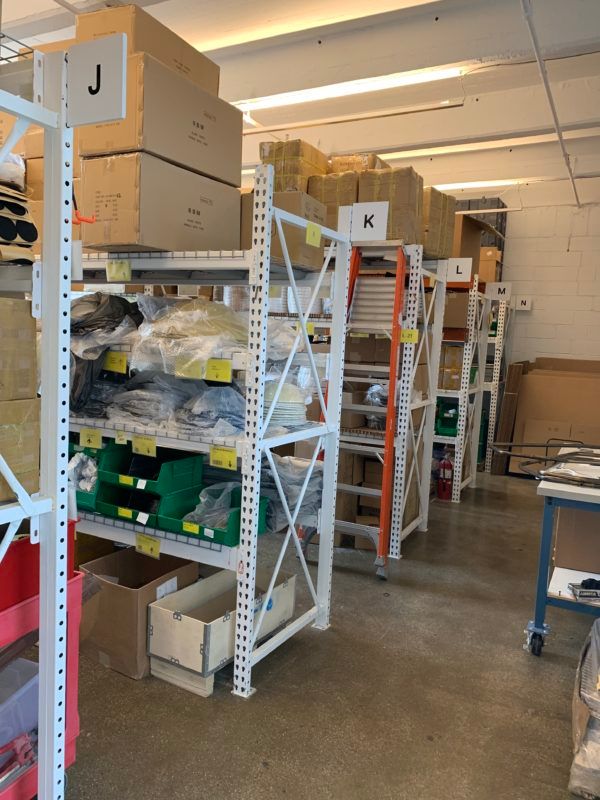
Shelving space even factors into their design process.
Once a customized order is finalized in their cloud-based software, their product specialists assemble each product meticulously in the workshop.
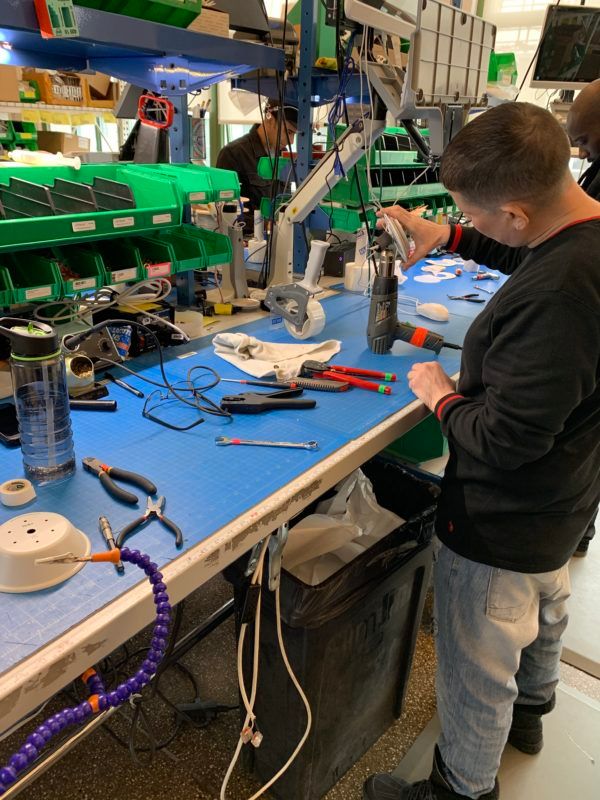
For instance, this…
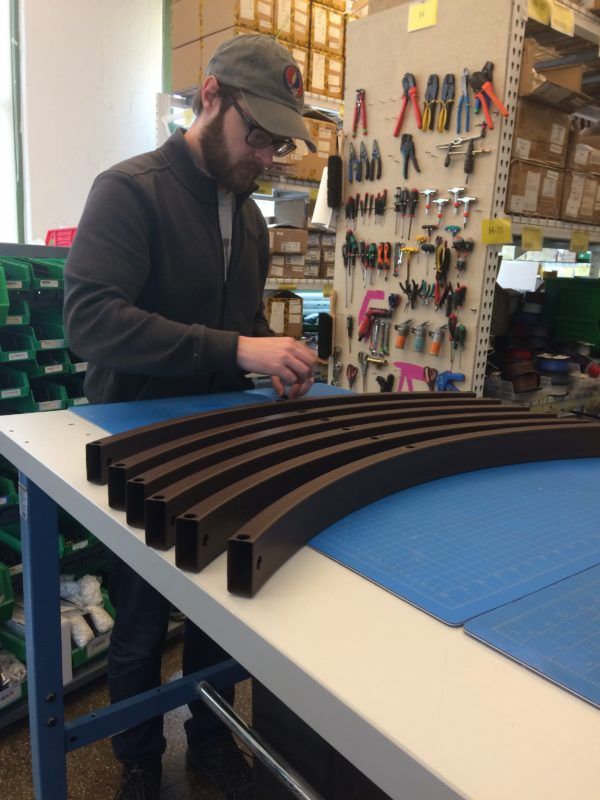
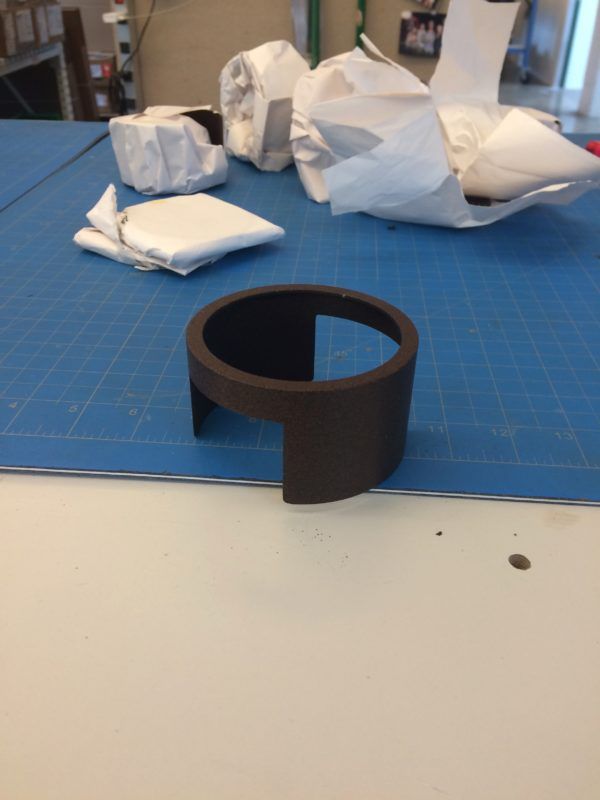
…will become a version of the Cinema chandelier:
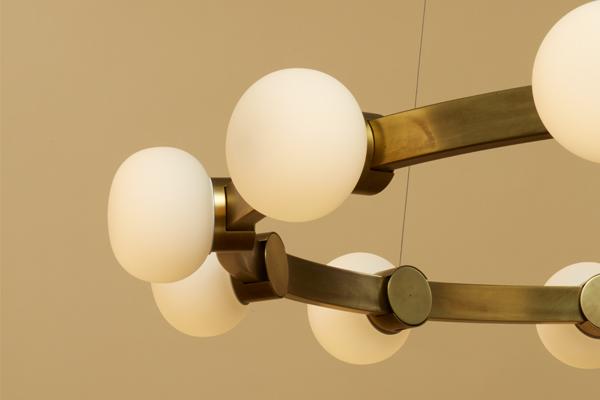
Like their products, the office side of RBW’s space is now streamlined and flexible, allowing for lots of different working and meeting configurations.
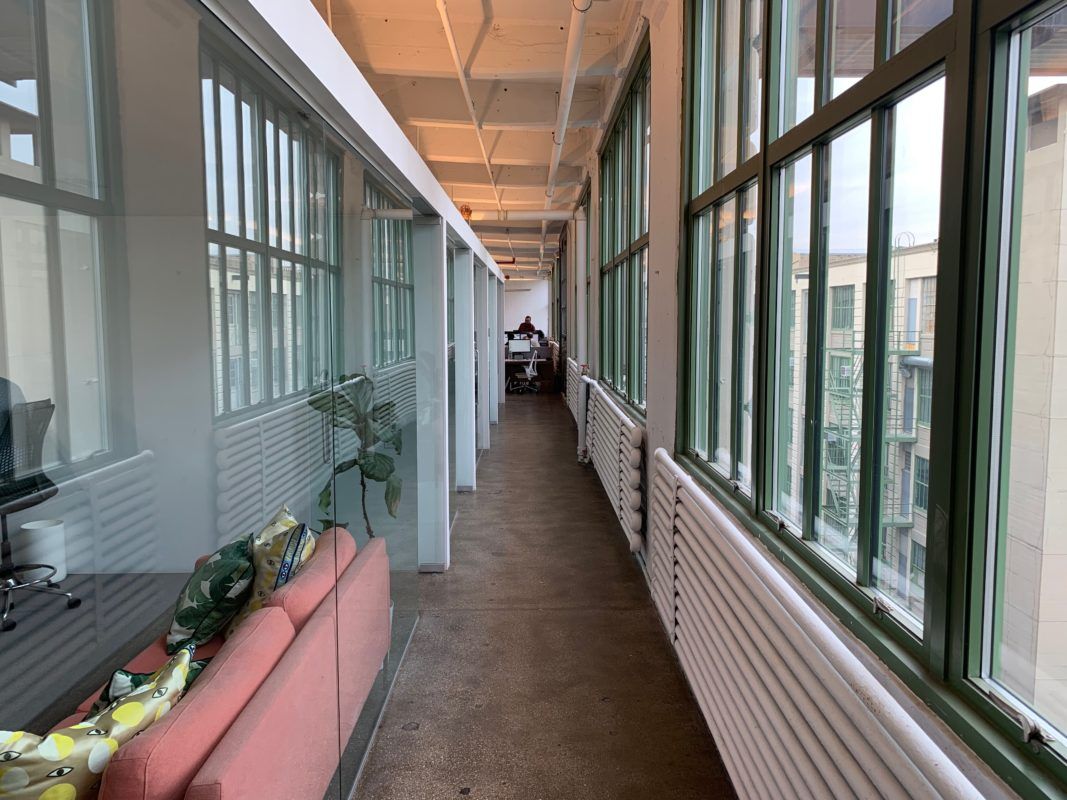
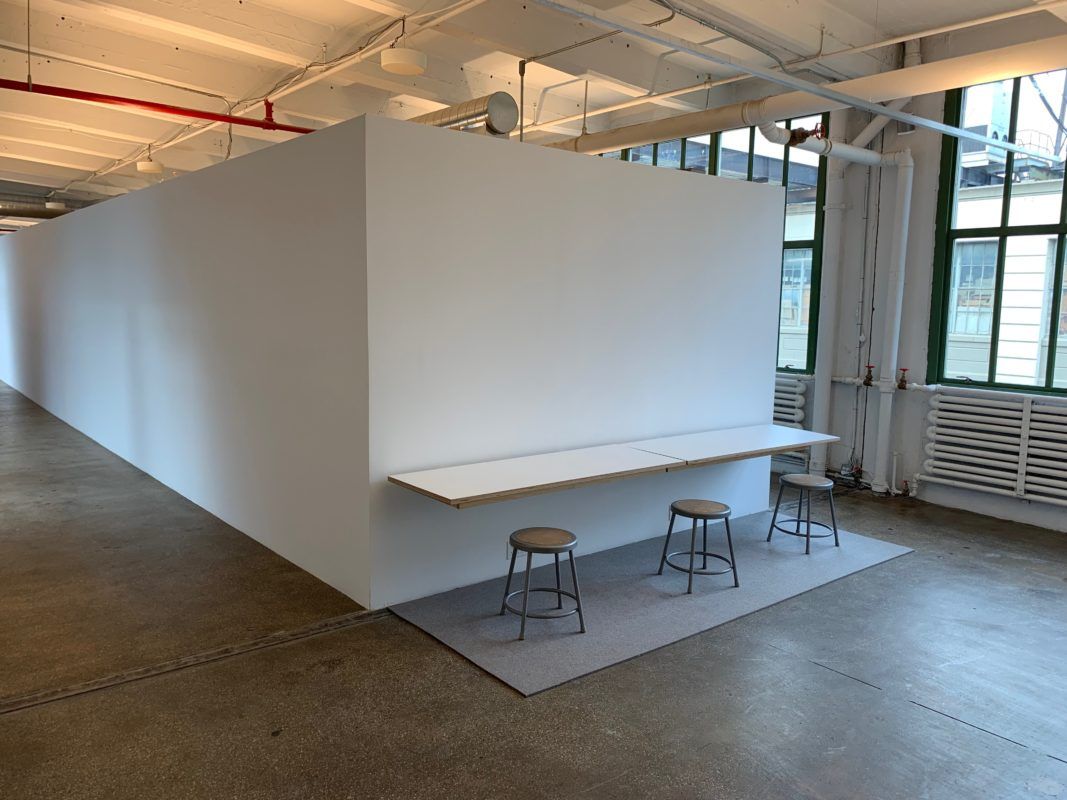
In between the two sides (“at the crossroads” as Theo puts it), is RBW’s developmental lab. There, they use 3D printers, cardboard, paper, foam, and a variety of other tools to mock up and test new design ideas.
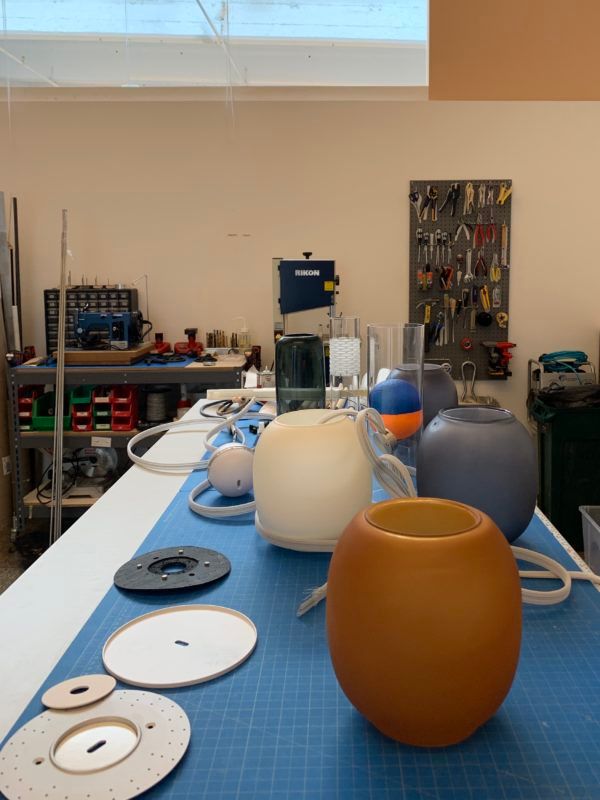
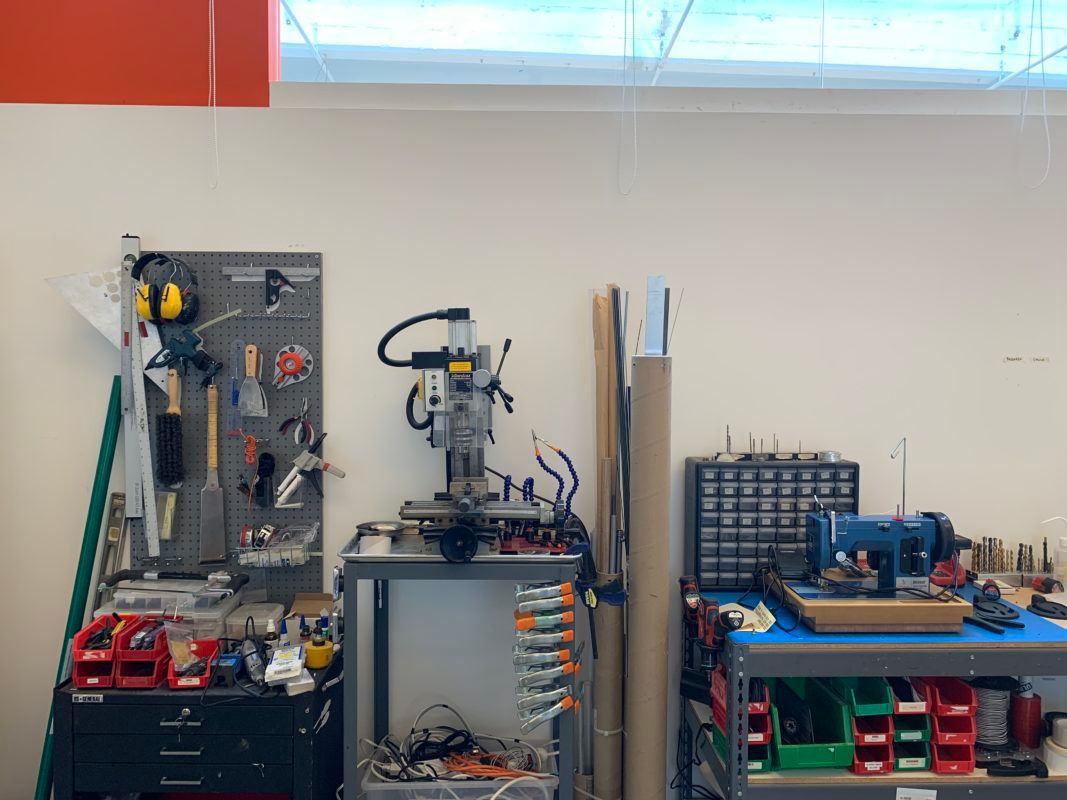
One of their recent designs developed here was Vitis, which has lights strung on a single continuous cord, which they custom designed and engineered. “We wanted to achieve a sense of translucency and atmosphere through ultimate dimming performance, like candlelight at its lowest setting, with a very gestural drape,” says Theo.
In pursuit of that, they played with various possibilities:
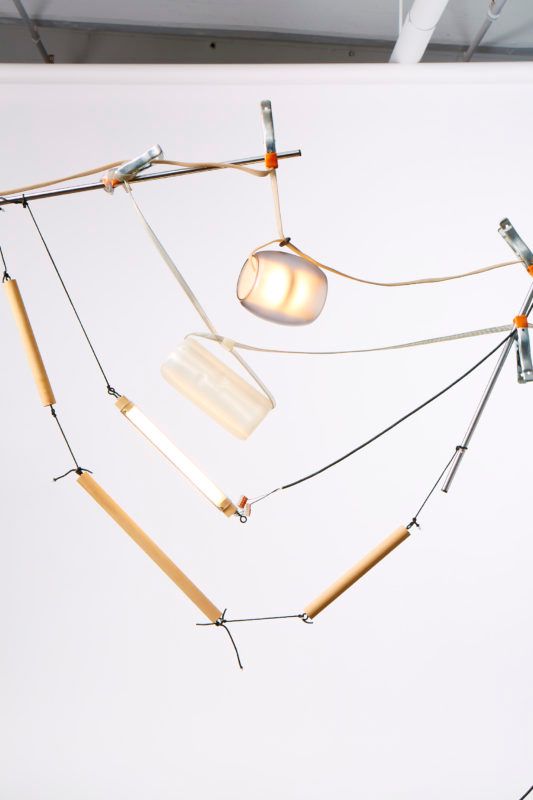
Ultimately, they settled on the design at top, like a beaded necklace:
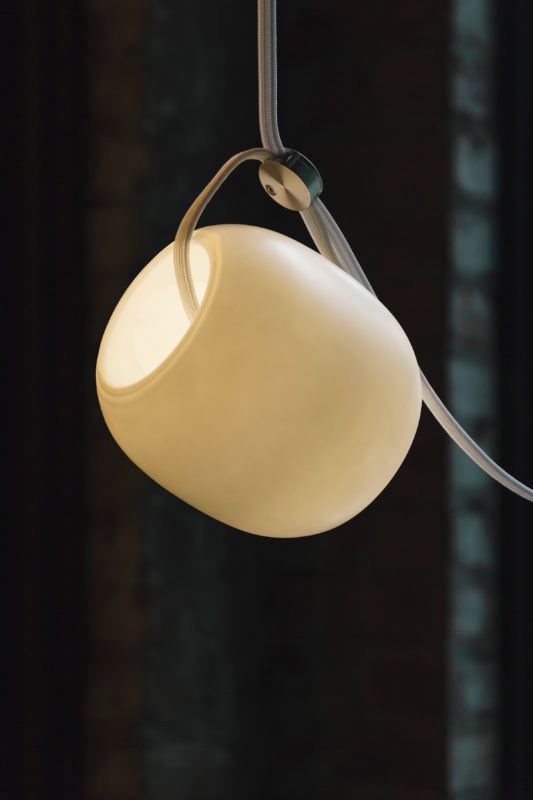
Currently, they’re working on new designs utilizing a variety of fabrics. They’ve used fabric in designs before, like in Delta:
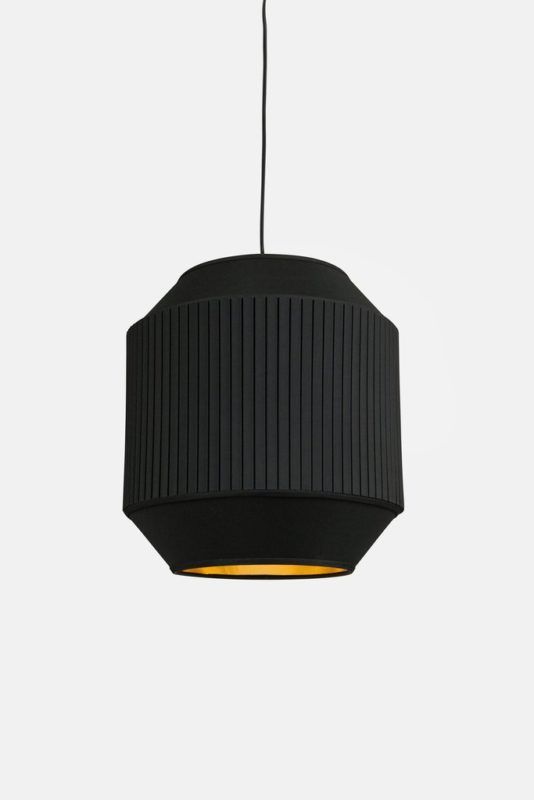
There’s a palpable creative energy beneath those three skylights in RBW’s newly configured workspace, and it’s not hard to imagine them needing even more room in another two years. But it’s also not hard to imagine that, when they do, Industry City will be there to help them along.
This post was sponsored by Industry City. If you would like to reach our readers, please contact us.